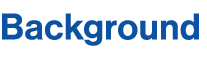
With a long history of proven expertise, APAC, Rinnai Australia’s commercial HVAC brand, continues to lead the market in delivering custom-engineered systems for mission-critical environments.
Designed and built in Melbourne, APAC’s HVAC systems are trusted across sectors including mining, defence, hospitals, shopping centres and large public spaces. Their in-house engineering and manufacturing capability enables responsive, high-quality solutions tailored for the Australian landscape. Thanks to a deep understanding of Australia’s harsh climate, APAC’s customised HVAC solutions have been the leading choice for many high-profile projects across Australia.
The Project Ceres Urea Plant by Perdaman Industries is a significant new chemical and fertiliser production site scheduled for completion in 2027. Located on the Burrup Pensinsula in the Pilbara region of Western Australia, this remote and challenging site required a highly robust HVAC system to ensure reliable performance in conditions such as extreme heat, dust and chemical exposure.
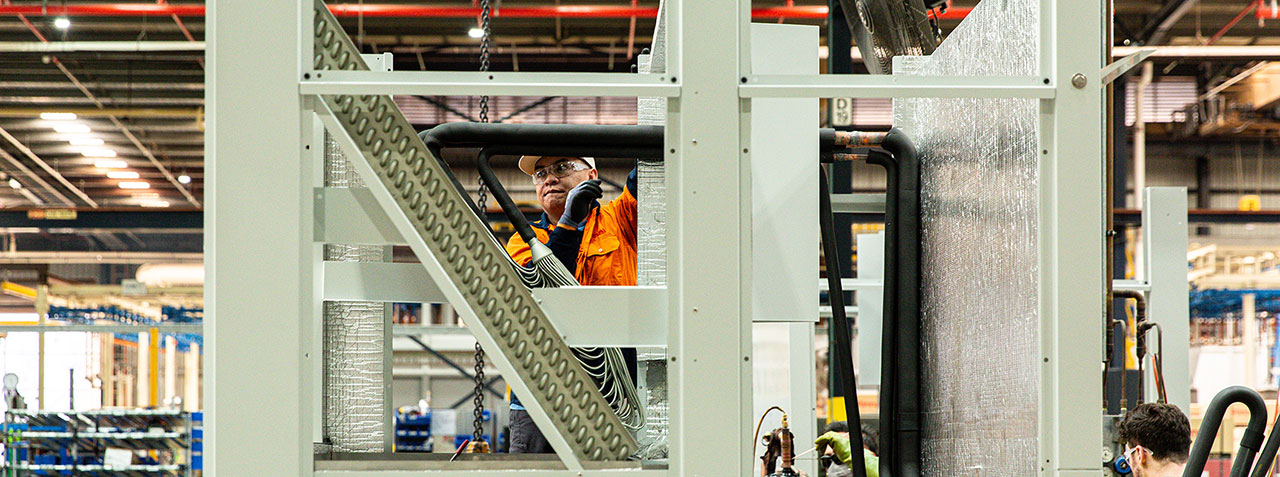
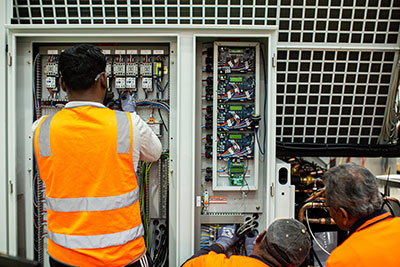
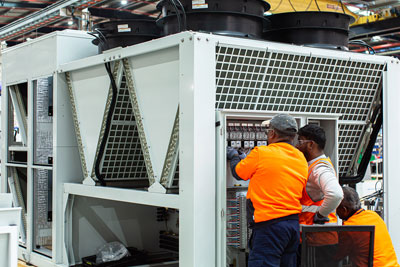
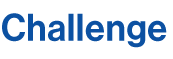
The Burrup Peninsula is known for being one of the most climatically extreme regions in Australia. High temperatures, corrosive salty air and frequent cyclonic weather conditions can seriously compromise the long-term performance, reliability and maintenance schedules of equipment such as HVAC systems.
Vital to operations at Project Ceres were the facility’s switch rooms which would require strict climate control to meet site-specific certifications and important safety, productivity and compliance standards. The chosen solution would undergo rigorous testing by independent auditors and certifiers.
“The unique environmental challenges of the site and high performance expectations of the project meant that a standard off-the-shelf HVAC solution wouldn’t be sufficient,” remarks Dale Watkins Group Manager – Commercial Sales, Rinnai Australia.
“And, as with many projects of this scale, timing was an important factor. The chosen HVAC solution needed to be designed, implemented and tested quickly to fit in with strict construction schedules.”
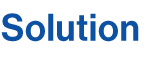
With a large manufacturing facility in Melbourne and a 236-person, dedicated in-house engineering and manufacturing team, APAC was the ideal partner to cater to the unique needs of the project. Local production allowed for tight control over design elements, quality and lead times.
In just 16 weeks from briefing, APAC designed, manufactured and delivered its largest and most powerful customised suite of HVAC units on record, comprising twenty-six 230kW systems, four 170kW systems and several smaller units.
These systems were manufactured across four production lines in the NATA-approved facility and were tested on-site to APAC’s stringent QA protocols to ensure every unit met or exceeded the required performance standards.
A key customisation to the units was the full 304-grade stainless steel casing with powder coating which offers enhanced corrosion resistance. Additional coil protection and a cyclone-resistant design ensure the systems are robust enough to withstand the site’s tough weather conditions.
Other tailored modifications included the use of German-engineered fans to meet airflow specifications and efficiency requirements as well as advanced filtration systems to maintain long-term performance in dusty, chemical-rich environments.
Close collaboration between APAC’s engineering team and the client was a key factor in the successful delivery of the project’s HVAC solution. From design through to commissioning, APAC’s local team held multiple planning and customisation sessions to ensure the solution met all operational and environmental criteria. They also worked alongside partners to manage timelines, delivery and final implementation.
“The solution that APAC delivered will ensure reduced maintenance costs, improved reliability and longevity in one of the world’s most demanding operational environments,” says Dale.
“We look forward to working with our partners to play an even larger role in the future of Project Ceres.”
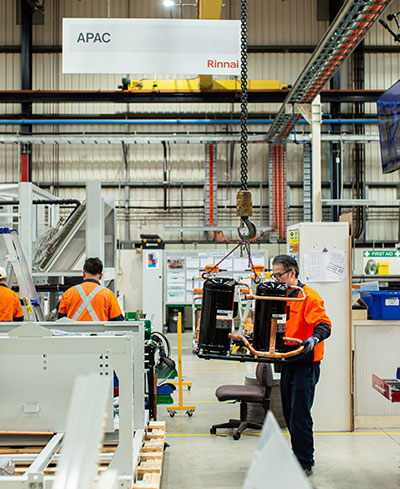